Additive Manufacturing by Gel-in-Gel Printing
DOI:
https://doi.org/10.31265/atnrs.778Abstract
Additive manufacturing by the 3D-printing processes enables solid free-form fabrication of three-dimensional objects directly from the digital images by melt prepolymers and gels following the post-curing of deposited polymers. Those processes have limitations due to long printing times, low-quality materials, and costs. The gel in gel printing by printing low viscosity materials in a support gel environment addresses those limitations. This process deposits a relatively low viscosity but curable liquids or gels into a medium of support gel. The support gel prevents the collapse or deformity of the printed object under its weight. Once the printing is completed, the object is cured, removed from the support bath, and rinsed off. The support gel can be reused. This sacrificial supporting gel has to be removed easily after 3D printing. There exists a very limited amount of materials suitable for printing and supporting the printed objects in a bath. Some of the support baths studied by different research groups are crosslinked polyacrylic copolymer microgels, granular gels, silica nanoparticle suspensions, and clay suspensions. The design of an appropriate supporting hydrogel bath poses several challenges. The supporting gel has to behave like Bingham plastic, not yielding until a threshold shear force is reached. In the meantime, its yield stress has to be low enough to accommodate nozzle movement. Besides supporting the deposited printing gel, the support bath must exhibit a high plateau shear elastic modulus, G ′. In addition, those viscoelastic properties have been thermo-reversible. Here, we discussed the role of yield stress of printing and support gels on gelling, shape integrity, and interlayer fusion.
References
Hajash, K.; Sparrman, B.; Guberan, C.; Laucks, J.; Tibbits, S., Large-scale rapid liquid printing. 3D Printing and Additive Manufacturing 2017, 4 (3), 123-132.
https://doi.org/10.1089/3dp.2017.0037
O'Bryan, C.S.; Bhattacharjee, T.; Hart, S.; Kabb, C.P.; Schulze, K.D.; Chilakala, I.; Sumerlin, B. S.; Sawyer, W. G.; Angelini, T. E., Self-assembled micro-organogels for 3D printing silicone structures. Science advances 2017, 3 (5), e1602800.
https://doi.org/10.1126/sciadv.1602800
Grosskopf, A. K.; Truby, R. L.; Kim, H.; Perazzo, A.; Lewis, J. A.; Stone, H. A., Viscoplastic matrix materials for embedded 3D printing. ACS applied materials & interfaces 2018, 10 (27), 23353-23361.
https://doi.org/10.1021/acsami.7b19818
Jin, Y.; Compaan, A.; Chai, W.; Huang, Y., Functional nanoclay suspension for printing-thensolidification of liquid materials. ACS applied materials & interfaces 2017, 9 (23), 20057-20066.
https://doi.org/10.1021/acsami.7b02398
Hinton, T. J.; Hudson, A.; Pusch, K.; Lee, A.; Feinberg, A. W., 3D printing PDMS elastomer in a hydrophilic support bath via freeform reversible embedding. ACS biomaterials science & engineering 2016, 2 (10), 1781-1786.
https://doi.org/10.1021/acsbiomaterials.6b00170
Hinton, T. J.; Jallerat, Q.; Palchesko, R. N.; Park, J. H.; Grodzicki, M. S.; Shue, H.-J.; Ramadan, M. H.; Hudson, A. R.; Feinberg, A. W., Three-dimensional printing of complex biological structures by freeform reversible embedding of suspended hydrogels. Science advances 2015, 1 (9), e1500758.
https://doi.org/10.1126/sciadv.1500758
Lan, X.; Liang, Y.; Erkut, E. J.; Kunze, M.; Mulet Sierra, A.; Gong, T.; Osswald, M.; Ansari, K.; Seikaly, H.; Boluk, Y., Bioprinting of human nasoseptal chondrocytes laden collagen hydrogel for cartilage tissue engineering. The FASEB Journal 2021, 35 (3), e21191.
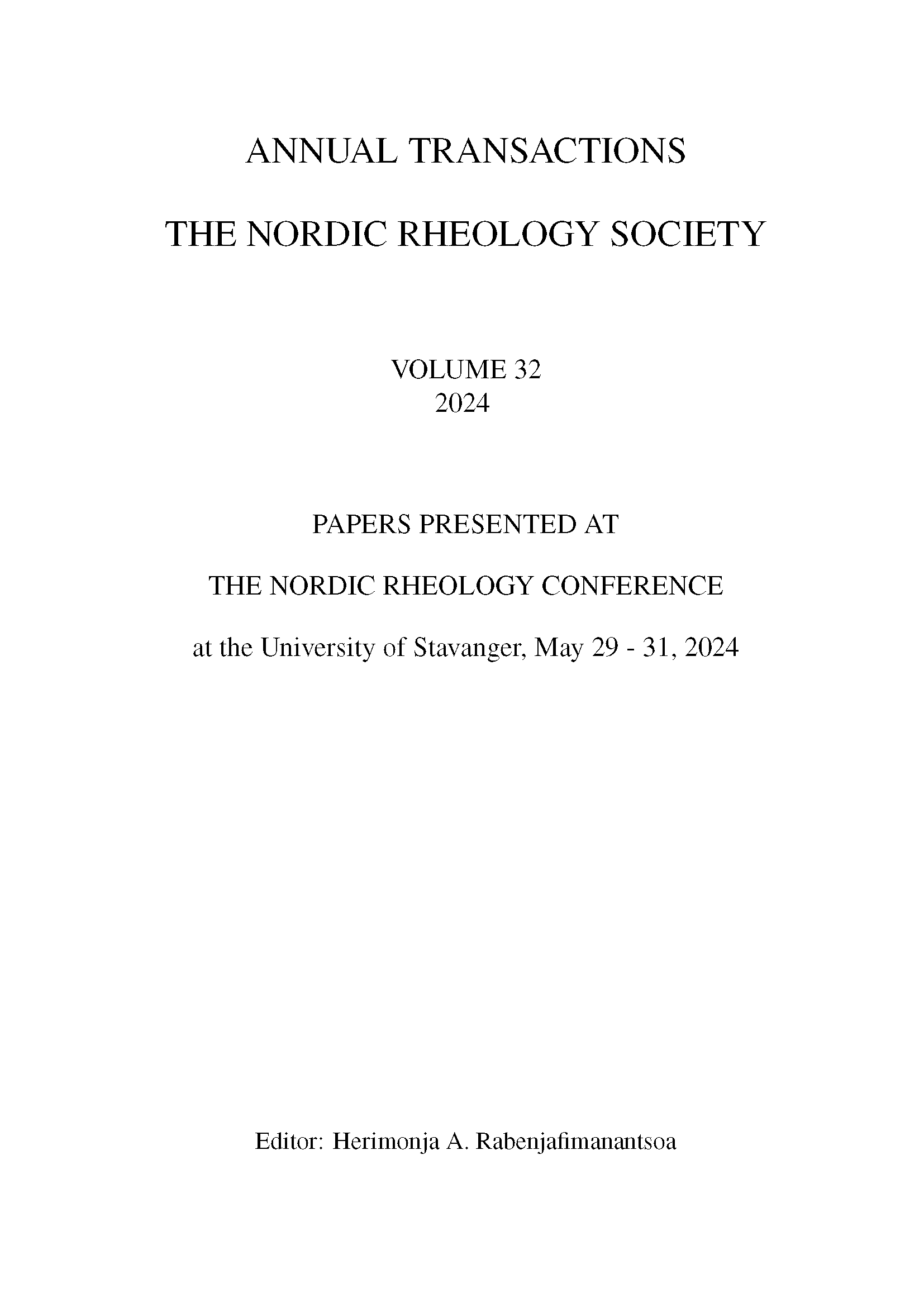
Downloads
Published
Issue
Section
License
Copyright (c) 2024 Yaman Boluk, Xiaoyi Lan, Adetola Adesida

This work is licensed under a Creative Commons Attribution 4.0 International License.